This article has originally been published here (German).
You have to write three emails in parallel, the slides for tomorrow’s presentation need to go out, the slack channel for the project is on fire and the calendar reminds you reproachfully of the team meeting. Wait, where did you put the browser tab with the important information you found ten minutes ago?
Who doesn’t know this modern working day with too many open tasks that never seem to be finished? In order to get a grip on this complexity of multi-tasking simultaneity, the Komplexitäter conducted an online workshop on June 24th, 2020, for our New Work Berlin community.
Workflows with obstacles
The three agile experts Andreas Lehmann, François Cannonne and Lars Nebe each moderated individual breakout sessions with about 10 participants. In an extremely entertaining 75 minutes, we learned how our intuitive assumption about how work should flow using a system can be quite off the mark. To visualize this, each participant had access to a virtual work simulation tool called Kanban Flow Simulator.
In each group, the workers were first allocated to work stations. Each individual gets a task in a virtual ship factory. This is a browser-based simulation of a production line, in which ships are drawn. Through this small, rather trivial activity the participants gain deep insights into organization and workflows. There are enough customer orders for ships in the backlog. Richard is the first to take an order from the backlog and draw in his browser: he lays the keel of the ship. When he has finished, he passes the order directly on to Luisa, who makes the deck and passes it on as well. Next, Jens straightens the mast, Marina carves the bow, and so on. After six stations the ship is finished and the customer’s order is completed. By the way, the last step is with Lisa, who manufactures the sail, which takes a little longer than for example the mast. Therefore the work orders start to pile up at Lisa. But more about that later.
After a small test run, the real work starts: The goal is to be as fast as possible. Intuitively, ships should move from workstation to workstation. There are always new orders coming from the backlog into the production line according to the FIFO principle – First In, First Out. We also work according to the push principle and thus push an order to the next station as soon as it is ready.
Every person is working as efficiently as possible on their own orders. Like every normal working day, we want to get the tasks away from our own desks as quickly as possible, and we are somewhat surprised to see that others are also piling up work. After four minutes of eager production, there is a stop in the simulation: the last customer order is marked and moves through the production line. There are still a few ships lying around at the stations and a bottleneck at the sail manufacturing step has become apparent. it takes some time until the marked last ship is finally finished.
Change from Push to Pull
The bottleneck is of course quickly noticed. At the stop, there are 12 unfinished ships lying around in the production line. This is the number of open orders our customers are waiting for: Work in progress (WIP). At the end of the day, all the workers are waiting for Lisa. She has to finish all the pending ships under high pressure until we can finally call it a day.
Our manager (one of the Komplexitäters) now changes the way we work in the system for the next simulated working day in two ways:
- We go from push to pull. That means, when I am done with my work, I wait for the person in the next production step to take my ship
- There can only be one ship at each station. We are introducing a WIP limit of one ship (1)
As the simulated second day begins, we quickly notice that there are more breaks. I can only continue working if my colleague takes my finished work to the next production step. So I simply have to wait from time to time. I feel that my own productivity suffers as a result. At the end of the four-minute working day, the last ship is marked again. However, this ship slips through the system quite quickly because there is no traffic jam at the bottleneck.
The benefits of Pull and WIP limit
On our first simulation day, we saw a traffic jam at the bottleneck. On the second simulation day, we had some breaks at the work stations. The kanban flow simulator has a key figure measurement, which we looked at together. Surprisingly, the throughput, i.e. the number of ships we manage per minute, is pretty much the same – despite the perceived break times at most work stations. This is because throughput is limited by the workstation that takes the longest. This is the bottleneck. The total throughput of a system is completely dependent on it.
The second key figure evaluated is WIP, work in progress. On the first day of the simulation, this metric rises steadily. Since new orders are pushed into the system and these orders are piling up at the bottleneck, a lot of work is lying around in the production line. In the second simulation, there is no traffic jam and there is only one unfinished product lying around at each station.
The kanban flow simulator shows the cycle time as a further key figure. While the cycle time increases steadily in the first simulation, it is quite constant at 80 seconds in the second round. What does this imply? In the first case, when the production system is up and running, we can hardly give the customer a prediction of how fast we can process the order, which is very unsatisfactory.
New Insights and Learnings
During the interactive evaluation we learned the following:
- With constant capacities, the cycle time increases for each additional order in the system
- If a station other than the bottleneck improves, it is even worse: the WIP increases and throughput still suffers due to the bottleneck.
- Every improvement at the bottleneck is an improvement to the overall system. For example, if a rare expert is working on the bottleneck, this expert should now be supported. Even if the support only possesses limited competencies compared to the expert working at the bottleneck, the throughput can still be increased.
- When a system is 100% utilized, traffic jams occur everywhere. The consequence is an absolute standstill and nobody is able to work.
In the past, smart managers collected all the information, understood the interrelationships and then made decisions. Today, with increasing complexity, this is hardly possible. Therefore, the New Work approach here is the optimization of the work system for the ability to change: short learn cycles, faster trialing and testing, constant learning and adaptation. Thus, the ability to change is built into the organization, as we could experience in our training.
We got quick feedback from the system, reduced the WIP and observed the throughput. We also noticed that the WIP-limited system gives us time for creativity, education or exploration. The Kanban Board is a management system to keep an eye on the whole situation. This visualization of the work process is the first step of the Kanban principle. Bottlenecks are quickly recognized and immediately become the place for optimization.
Our guest authors
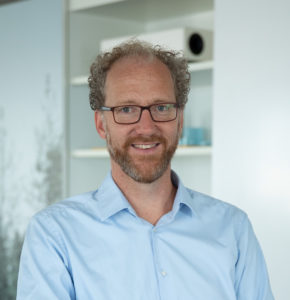
Jens Hündling – picture by studioafraz.com
Jens Hündling is a freelance trainer and coach for digital transformation and new work. As a former IT executive, he prefers to communicate with people rather than machines. Jens is passionate about developing teams and organizations. Especially with East Frisian humor. More about him at https://dr-huendling.de
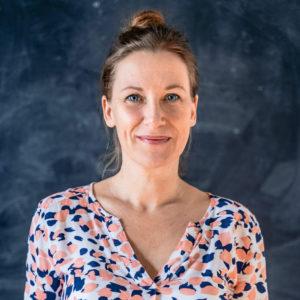
Heidi Dommaschke
Heidi Dommaschke accompanies people and organizations in change as trainer, mediator and coach. In addition to inner work, resilience and resource development, she is particularly interested in the further development of communication and conflict competence. In doing so, she is concerned with the question of how we want to live and work, and how we can actively shape the world around us. https://www.hundred-ways.com
Featured Image by Freepik.